Associates
We undertake initiatives to enable associates to work safely and with peace of mind and to allow diverse human resources to exercise their potential and play active roles.
Human Resources Management and Labor Management
Basic Concept
Toyota Industries undertakes a range of initiatives based on our basic perspective to develop and leverage the capabilities of associates and the organization to the fullest by promoting the creation of a highly motivated team.
Increasing Work Motivation
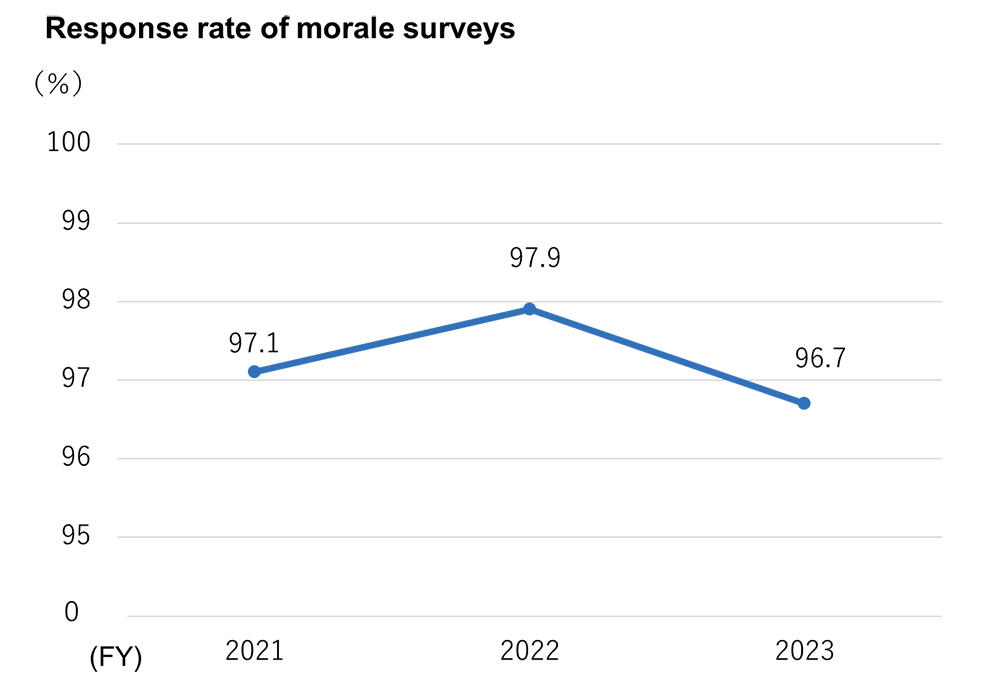
It is essential to create an open workplace so that individual associates can fully demonstrate their abilities in their own ways and find their work rewarding and meaningful.
At Toyota Industries, supervisors and more experienced associates have been taking the lead in creating a workplace culture that allows members to freely share opinions and suggestions. They also work to establish a relationship so that they can sincerely work to solve difficulties or troubles faced by members. To this end, we are making Companywide efforts and holding labor-management discussions throughout the year.
We also conduct an annual Company-wide morale survey to listen to voices of associates. Survey topics cover various aspects, including workplace culture, an individual’s willingness to grow and growth achieved and supervisors’ management of subordinates. By doing so, we clarify issues and required measures and make efforts accordingly.
Nurturing Human Resources and Promoting Active Roles
It is crucial to build a flexible and robust organization that can adapt to future uncertainties and various changes. Accordingly, we strive to nurture human resources who can trigger changes in the surrounding environment and themselves and back up associates tackling challenges.
On-the-Job Training (OJT)
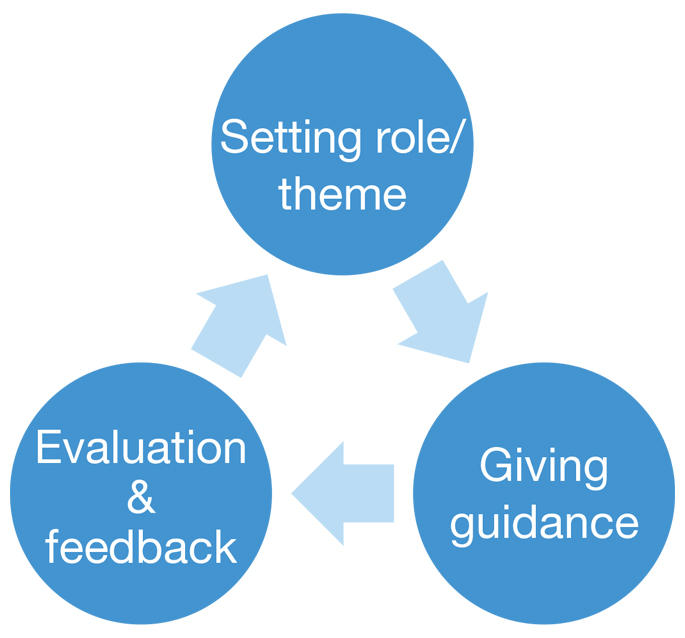
We engage in human resources development in each workplace with a focus on the OJT cycle consisting of three steps: setting a role and theme for each associate, giving guidance and providing performance evaluation and feedback.
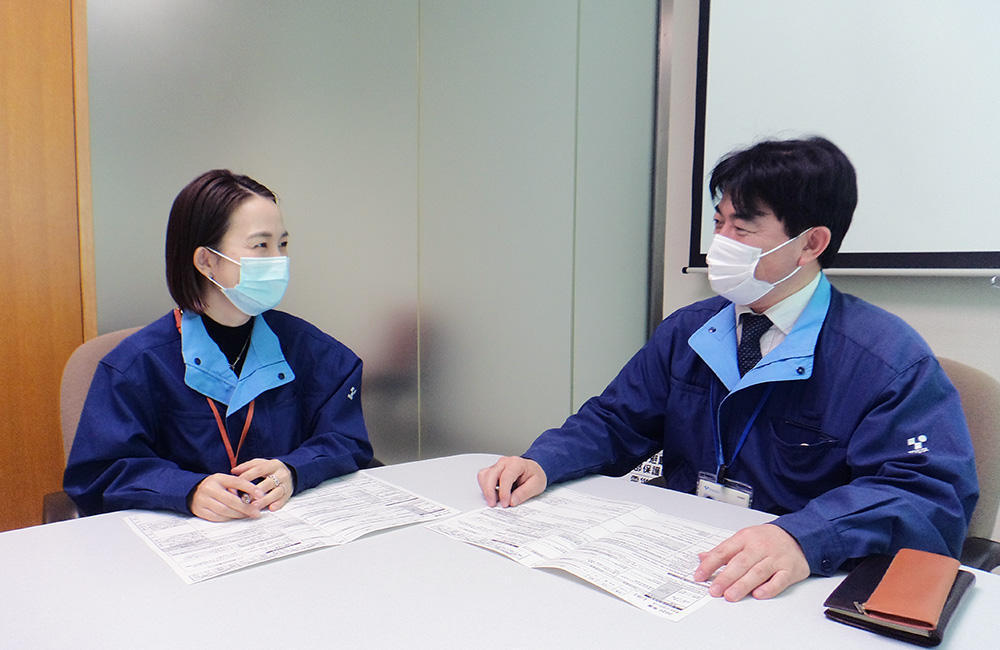
Specifically, a supervisor and subordinate hold discussions to determine an aspired role and theme at the beginning of a fiscal year. After laying down the growth expectation and target for the subordinate, the supervisor gives guidance on a daily basis. At semiannual interviews, the supervisor gives feedback to the subordinate on his or her strengths and areas of improvement. The cycle leads to further growth and a more active role of each subordinate.
Going ahead, we will introduce a 360-degree feedback system designed to encourage the growth of supervisors. Through the system, we will provide an opportunity for them to reflect on their actions and facilitate behavioral change.
As additional efforts to support autonomous career development, we will establish a system for associates to submit their aspired growth and role to their respective workplaces and enhance our internal job posting system that allows them to apply for a desired job.
Off-the Job Training (Off-JT)
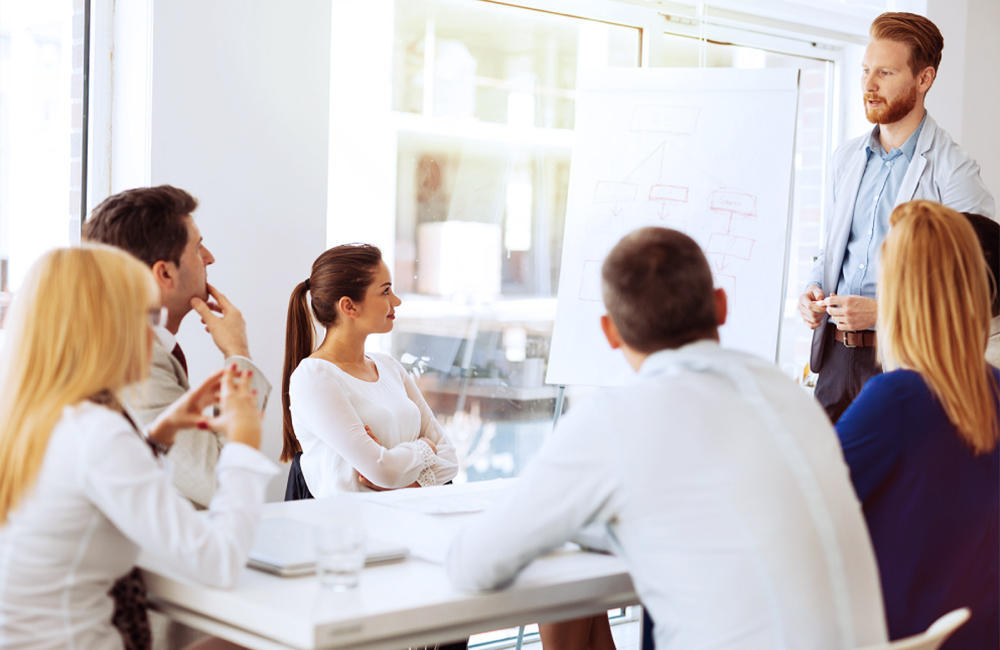
We provide various training programs that are practical and useful in the workplace, including induction training for new associates, training for newly promoted associates and seminars to gain specialized knowledge or capabilities. These programs are also made available to associates of affiliated companies in Japan.
We also engage in the development of human resources globally with a focus on the following three pillars.
(1) Global leader training
(2) People-to-people exchange (temporary overseas assignment, overseas training and Intra-Company Transferee (ICT) system to accept associates of Group companies outside Japan)
(3) Training to be held at Group companies outside Japan to cultivate a sense of value shared across the Toyota Industries Group
■Annual training hours per associate: 6.1 (fiscal 2023)
Support for Personal Development
We provide opportunities and venues for personal development and voluntary study to increase associates’ willingness to expand their knowledge and perspective and to learn independently. We also provide financial aid to support their personal development.
Work Styles without Time or Place Constraints
To enable associates to work productively, we are working to create systems and an environment for them to work flexibly without time or place constraints. To offer more diverse work style options, we have enhanced our telecommuting system in addition to establishing a flex time system without corehour requirements, satellite offices and a discretionary work system.
Supporting Active Roles of Diverse Human Resources
For generating new value by flexibly responding to the changing business environment and diversifying customer needs, we aim to create an organization that allows human resources that are diverse and proactive to exercise their abilities to the fullest and make accomplishments through co-creation.
We are promoting initiatives to realize a corporate culture in which associates accept and respect each other’s differences, including gender, age, nationality, race, religion, sexual orientation, gender identity, disabilities, experience, sense of value or any other invisible difference.
Empowerment of Female Associates
We aspire to let individual associates take active roles regardless of gender. Accordingly, we have been undertaking a range of initiatives from various aspects, such as changing mindsets, providing career support for female associates and promoting flexible working practices.
In seeking to ensure that female associates engaging in production operations fully work and take active roles until an older age, we also hold a work style seminar for female production associates and a seminar for supervisors on nurturing female subordinates.
As a result of these efforts, Toyota Industries received Japan’s “Eruboshi” certification and an “Excellent Company” award under Aichi Prefecture’s “Female-Friendly Company” certification program.
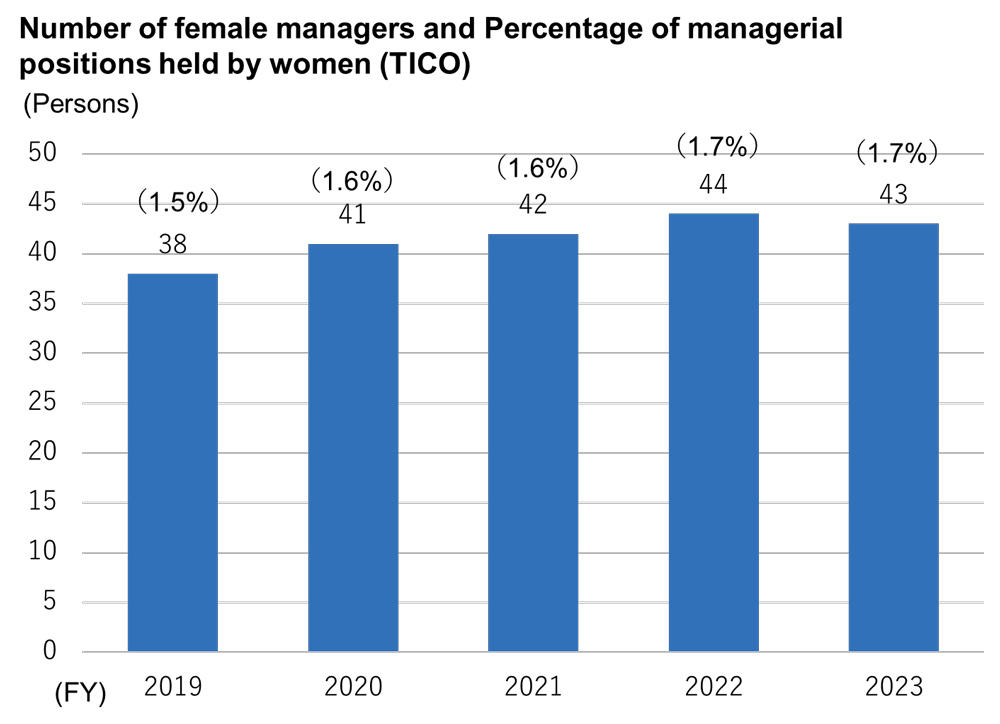
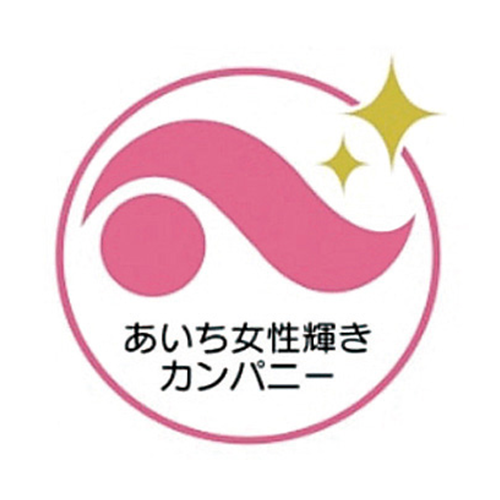


Targets and Major Initiatives for Promoting Active Roles of Female Associates
Target 1 | Ratio of female managers: Double the ratio to 2.4% in fiscal 2025 and triple it to 3.6% in fiscal 2031 compared with fiscal 2015 when the target was defined | |
---|---|---|
Result | 1.7%, or 1.4 times the fiscal 2015 level (as of March 31, 2023) | |
Example efforts |
Awareness-raising seminars for managers; training for career development for female associates; formulating and implementing individual development plans; role model exchange meetings; pre-maternity leave seminars; installing delivery lockers in-house |
Target 2 | Ratio of female graduate recruits: 40% in office work positions and 10% in engineering positions | |
---|---|---|
Result | 57% in office work positions and 8% in engineering positions (among new hires in April 2023) | |
Example efforts |
Recruitment events for female students; participating in initiatives of the Toyota Female Engineer Development Foundation |
Target 3 | Ratio of male associates taking parental leave: 30% in fiscal 2026 | |
---|---|---|
Result | 32.5% (fiscal 2023) | |
Example efforts |
Encouraging associates and their spouses to participate in pre-maternity leave seminars; internally communicating our parental support systems and example support for a work-life balance |
Initiatives for Persons with Disabilities
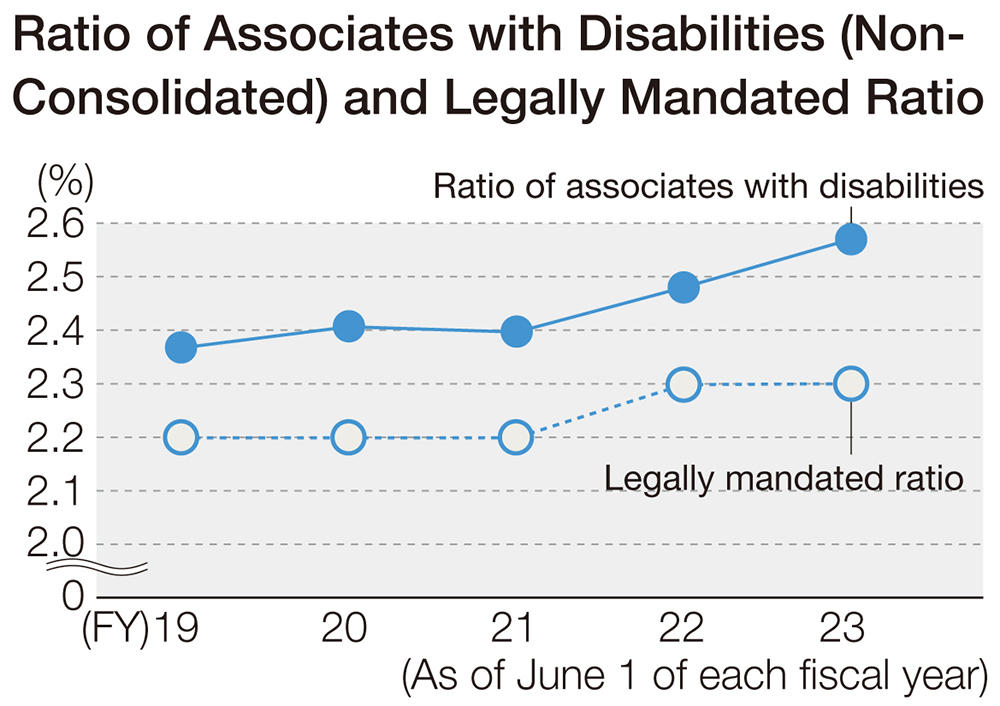
We respect the idea of people with and without disabilities working together and sharing life and work values. Under this basic policy, we continue to employ persons with disabilities every year. In order to ensure that they receive fair opportunities for achieving growth and taking active roles after joining Toyota Industries, we dispatch sign language interpreters when they receive training, provide tools to support communication and assign counseling staff.
■Ratio of associates with disabilities: 2.57% (non-consolidated)
Creating an Age-Inclusive Workplace
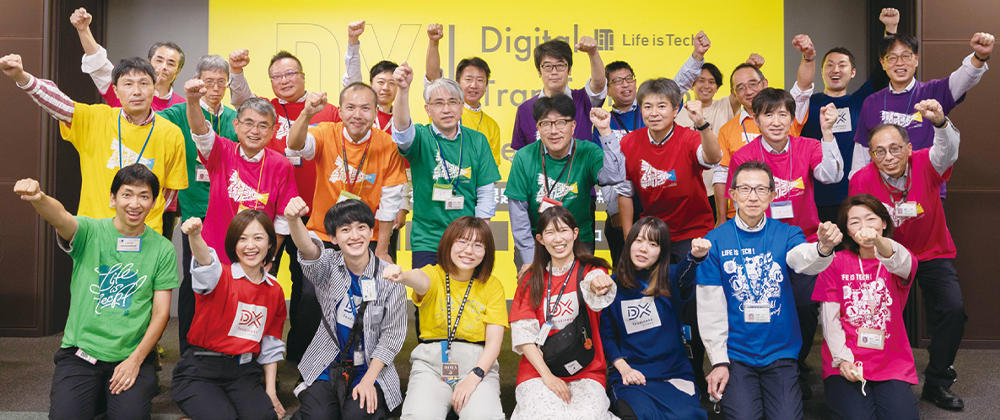
We provide practical digital skills education for experienced associates, who have broad work experience and perspectives, to learn the knowledge on digital technologies and know-how to use them through themed practical work in the workplace. They cultivate knowledge and skills through education and contribute to the workplace by actively promoting the use of digital technologies after finishing their education.
In order to enable older associates to work and take active roles in production operations, we have been creating better, less physically stressful production lines for them. Efforts include setting up standards for the handling of heavy objects and a work environment that makes it easier for older associates to work, and improvement in processes in production lines using digital technologies.
Supporting Work-Life Balance
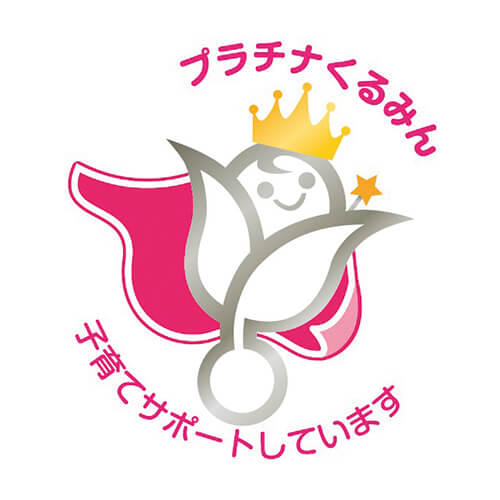
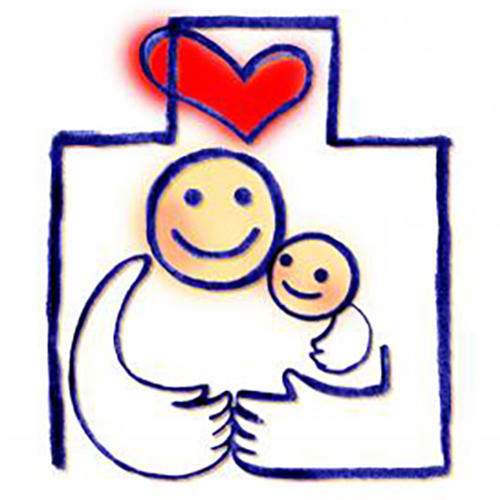
We have been carrying out activities so that associates who are balancing work and family can work with higher motivation and pursue career development. Such activities mainly focus on enhancing systems to support a work-life balance and facilitating an understanding for maintaining a work-life balance.
As a result of these efforts, Toyota Industries received “Platinum Kurumin” certification and won a “Family-Friendly Company” award.
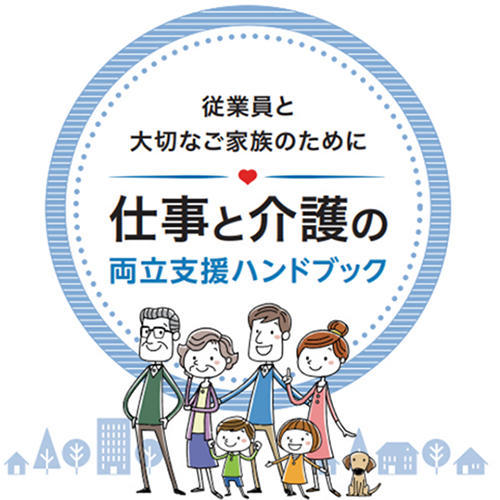
Enhancing systems to support a work-life balance |
Establishing in-house daycare center; shorter work-hour system for childcare; leave system and loan system for fertility treatment; return-to-work system to reinstate associates who have left work to provide child or family care or to accompany their spouse for a job transfer, etc. |
---|---|
Facilitating an understanding of maintaining a work-life balance |
Distributing the Handbook for Balancing Work with Nursing Care; distributing the Handbook for Balancing Work with Family Care; seminars on balancing work with nursing care; providing newsletters on nursing care, others |
Working with Colleagues from Different Countries
We have been undertaking business outside Japan for many years and now have 236 overseas bases, of which more than 200 companies are led by a local president. In addition, some 50,000 associates are engaging in business activities outside Japan, accounting for about 70% of all associates of the Toyota Industries Group.
Efforts for Mid-Career Recruitment
We have been reinforcing mid-career recruitment to incorporate external knowledge. In fiscal 2024, we plan to increase the ratio of mid-career associates in office work and engineering positions to 30% of all main career track associates (20% in fiscal 2023). Mid-career associates are assigned to their desired business divisions or job categories and after finishing induction training, take active roles in each workplace.
Safety and Health
Basic Perspective
Based on the idea of building “a homelike atmosphere at work that is warm and friendly” as stated in the Toyoda Precepts, we formulated the Safety Vision in 2013 after holding repeated discussions on the “basic stance on safety” and “optimal safety we seek.” The vision has been instilled at all bases in the Toyota Industries Group.
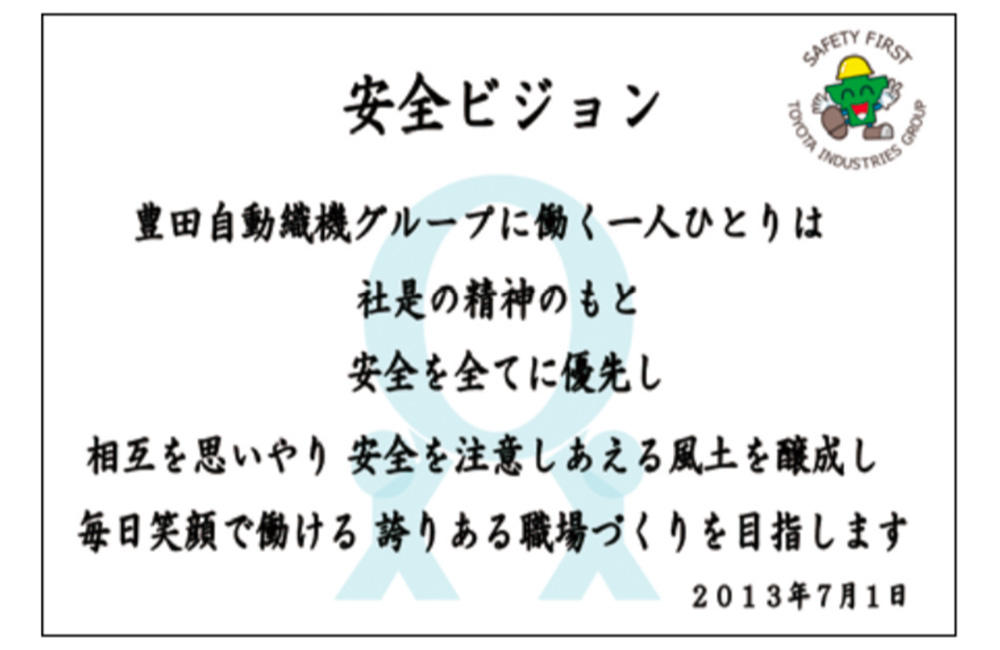
Safety Vision Each and every associate in the Toyota Industries Group, guided by the spirit of our corporate creed, aims to create a corporate culture that places a top priority on maintaining safety in all areas and focuses on mutual courtesy and safety as well as realizing workplaces where associates work each day with a sense of happiness and pride. |
---|
Structure for Promoting Safety and Health
Under our basic policy of placing a top priority on safety and health, we have been striving to eliminate accidents and occupational disorders. As part of such efforts, we have established the necessary committees, including the Central Safety and Health Committee and Plant Safety and Health Committees.
Occupational Safety and Health Management System
In accordance with the concept of an Occupational Safety and Health Management System (OSHMS/ISO 45001), we have established a required management structure in each plant (or business division) headed by a general safety and health manager (senior executive officer or another executive) and have been achieving improvements in safety and health activities on an ongoing basis from human, object and administrative standpoints based on risk assessment.
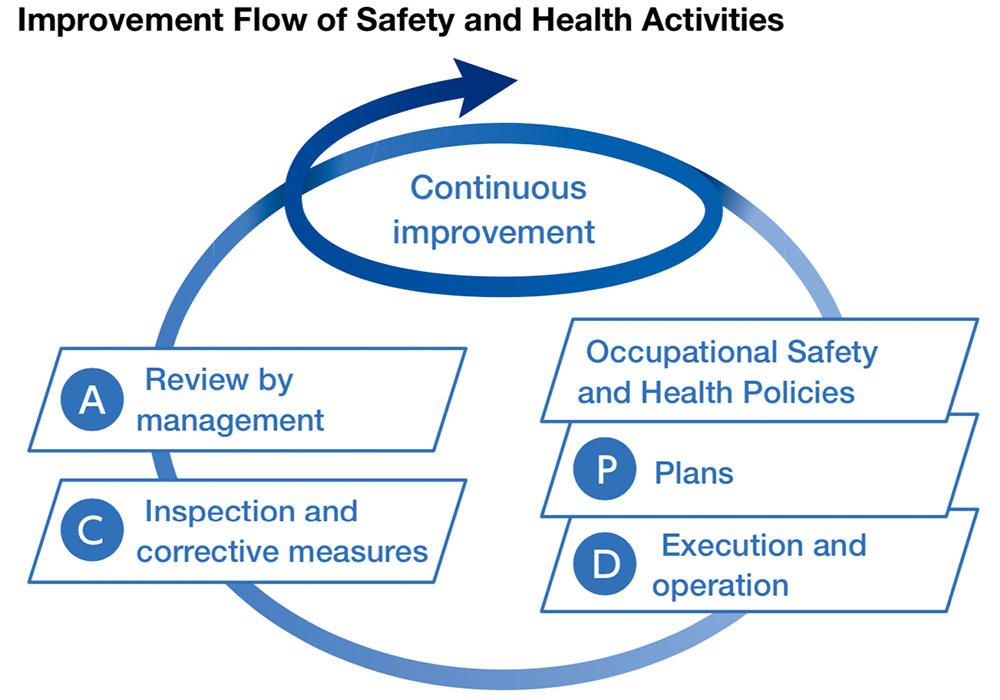
Prevention of Accidents and Disorders through Safety and Health Education
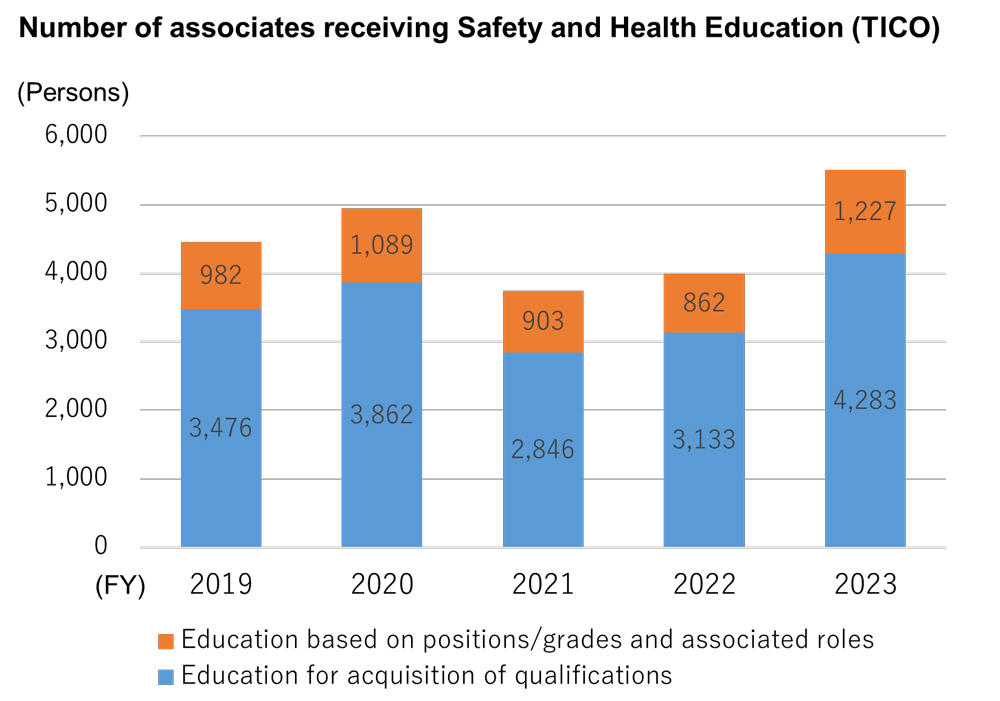
In order to cultivate knowledge, awareness and the skills necessary to prevent accidents and disorder, Toyota Industries proactively provides safety and health education, including education required by law to cultivate relevant knowledge and skills and to raise safety and health awareness, in addition to grade-based education and job-category-based education. Through these efforts, we are promoting the development of human resources and workplaces that places the highest priority on safety.
- Acquire qualifications (cultivate personal skills)
Licenses; skills seminars; special education; repeated education for capability improvement - Raise safety and health awareness
Education to improve ability to predict hazards; education to actually experience hazards (safety dojo) - Prepare for roles associated with positions/grades
Induction training; training for third-year production associates; training for newly promoted senior experts and chief experts; training for newly promoted experts; safety manager education - Prepare for job categories and business characteristics
Education on emergency measures; education on equipment lockout; education for equipment safety inspectors; hands-on safety education using virtual reality (VR)
Creating a Safe Workplace by Preventing Occurrence and Recurrence of Industrial Accidents
Since the occurrence of a serious accident in 2019, we have been working to eliminate accidents related to powered machinery and constantly upgrading our physical and administrative measures. Specifically, we have incorporated into our new and existing equipment a mechanism that cuts off power whenever an operator accesses a machine with its safety device disabled. We have also rebuilt our equipment safety assurance system. The system includes a visualization of which parts of the equipment are shut down, the control category under which it is operating and safety feature checks by qualified equipment safety inspectors.
Moreover, to make further efforts toward zero accidents, we believe that it is important to prevent accidents caused by the unsafe behavior of operators themselves, including taking a shortcut, omitting a step in a particular work process or showing disregard for safety. In fiscal 2023, as part of human-related measures, we started undertaking an initiative to quantitatively assess the tendencies of individuals, namely risk perception and risk-taking attitude*1. We will keep carrying out this initiative to prevent accidents caused by human factors.
We will continue to work toward the development of safe workplaces and safety-oriented human resources based on an approach to always shut down a machine when something is wrong and take fundamental measures to remove the root cause.
*1
Risk perception: An ability to recognize a risk as a risk
Risk-taking attitude: Tendency to intentionally accept a risk and act accordingly even when one perceives the risk
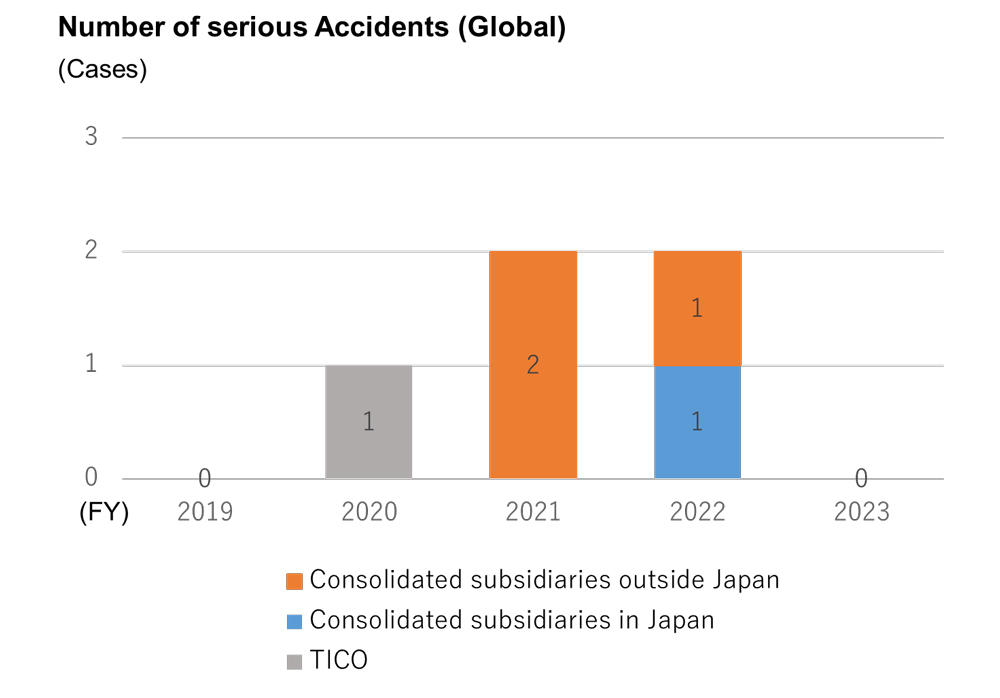
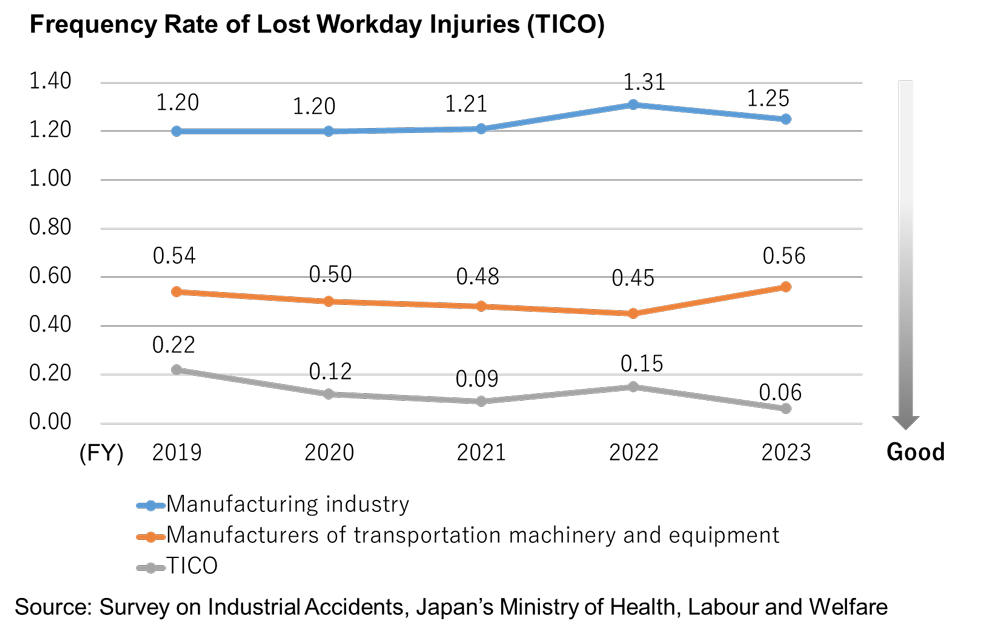
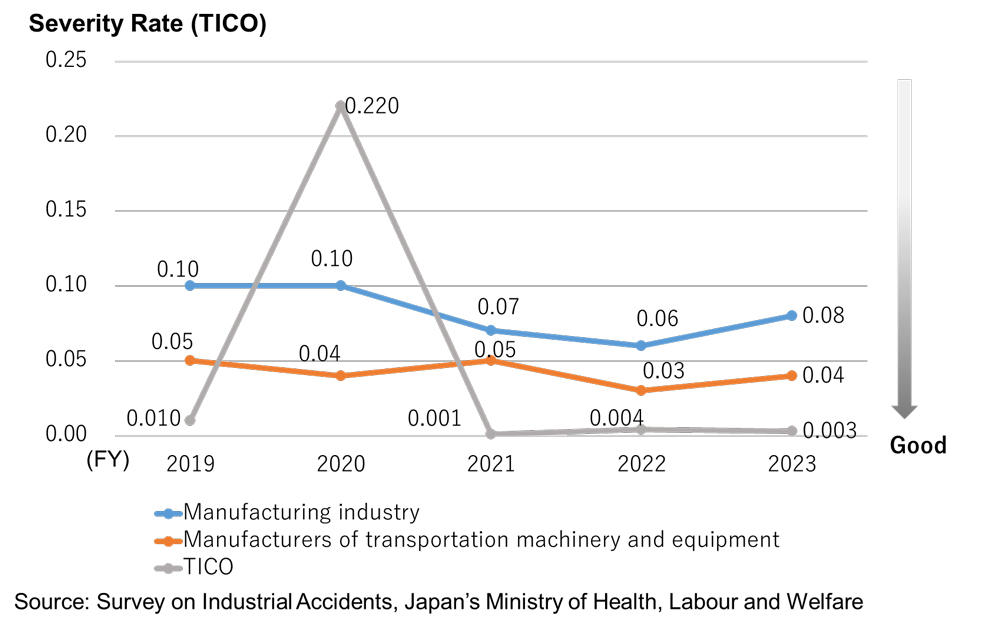
Health
Basic Perspective
As a task for the medium term, we are promoting health improvement of associates, mainly focusing on the prevention of lifestyle diseases and mental health support activities, to counter risks of health problems associated with aging and greater stress. To enable associates to work and take active roles over the long term, we provide support toward the cultivation of an autonomous health-oriented culture in which associates care about their own health and take action voluntarily and willingly.
Prevention of Lifestyle Diseases
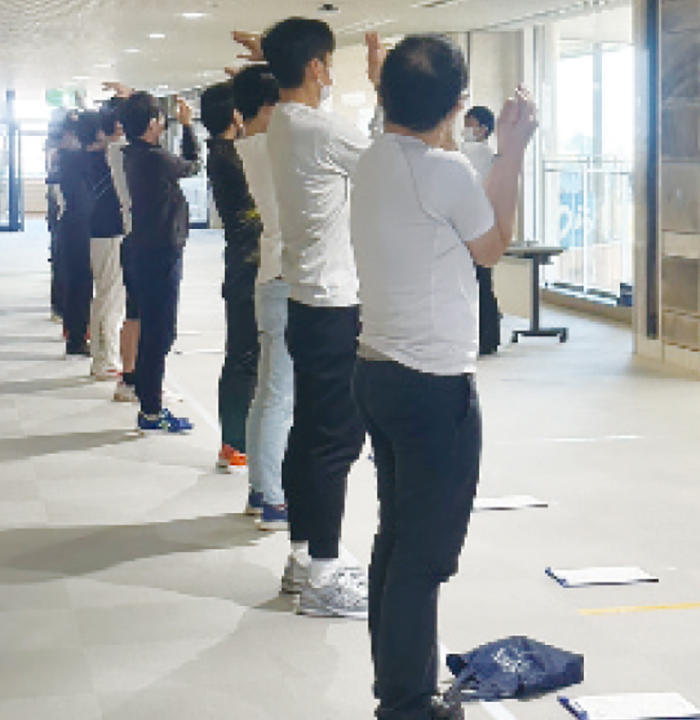
As a collaborative initiative of Toyota Industries, its workers’ union and health insurance association, we conduct periodic age-based health education for all associates (every five years, from the age of 30) and offer a Milestone Health Class as part of this education. To provide motivation for better health, we feed back to associates the results of an annual health checkup along with advice to improve lifestyle habits. In fiscal 2020, we started providing such information as physical fitness propensity scores and countermeasures, how physically fit for work, assessment of physical fitness age and recommended exercises to increase motivation for promoting physical fitness.
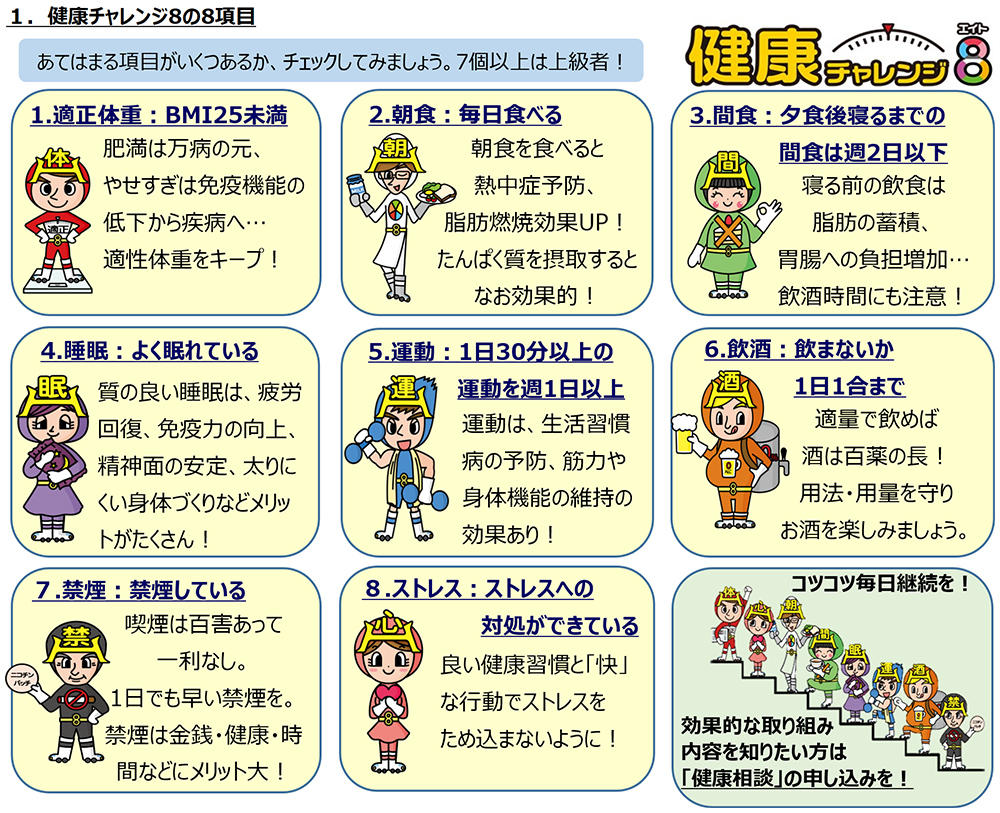
Since fiscal 2022, we have been promoting the “KENKO Challenge 8 (8 Challenges for a Healthier Lifestyle)” initiative to promote the cultivation of appropriate lifestyle habits in daily lives by defining eight lifestyle habits and giving each a score. In fiscal 2023, we took two approaches to instill the initiative among associates and increase their health literacy*2, the two pending issues from fiscal 2022. One approach targeted individuals, and we provided health-related information to encourage behavior change, along with the results of a KENKO Challenge 8 survey. As for the other approach covering the entire Company, we focus on conveying the meaning of the initiative and providing information on workplace programs to improve each of the eight lifestyle habit items through meetings of the Plant Safety and Health Committees.
With a declining labor force and aging society, it is essential to maintain the physical fitness of associates. However, the score for “Exercise” was lower than other lifestyle habit items defined in the initiative. In response, we will promote various efforts and initiatives to encourage associates to exercise during a short break or after work.
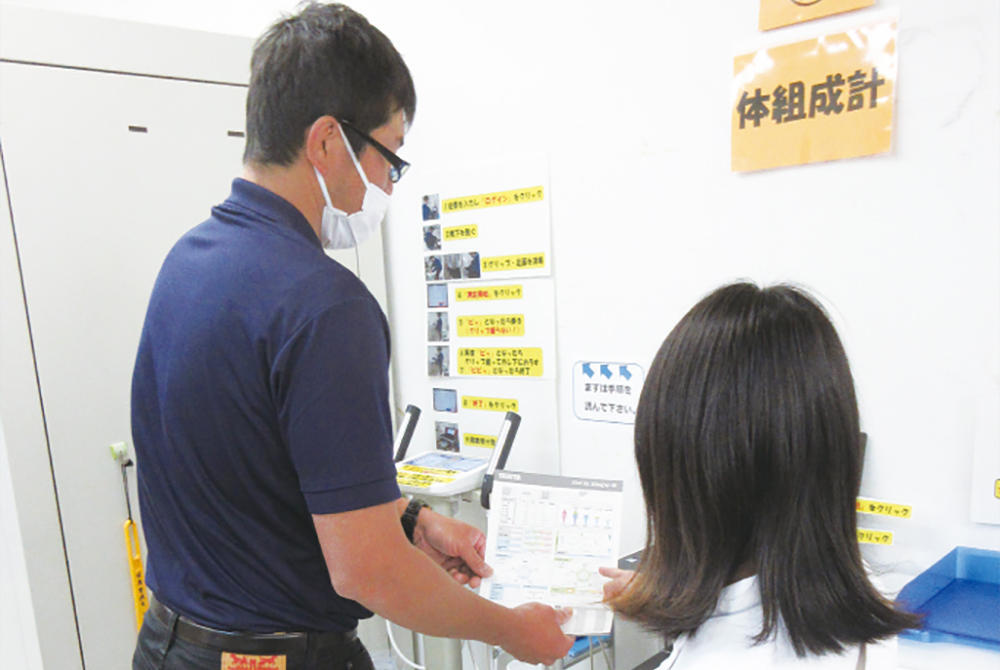
To prevent and ameliorate metabolic syndrome, we implemented a new weight reduction program that uses a body composition analyzer (BCA), in addition to providing the Milestone Health Class and health guidance to associates whose body mass index (BMI) is above 25.0. The program has led to reductions in the body-fat percentage and visceral fat level as well as behavior change among the participating associates. Some participants noted the use of a BCA makes it easier to see a difference (or a positive effect) as it visualizes their body shape. We plan to use a BCA in annual health checkups and health guidance to raise associates’ interest in changing themselves and provide better motivation for their behavior change.
*2: Knowledge, willingness and ability to obtain, understand and utilize health-related information
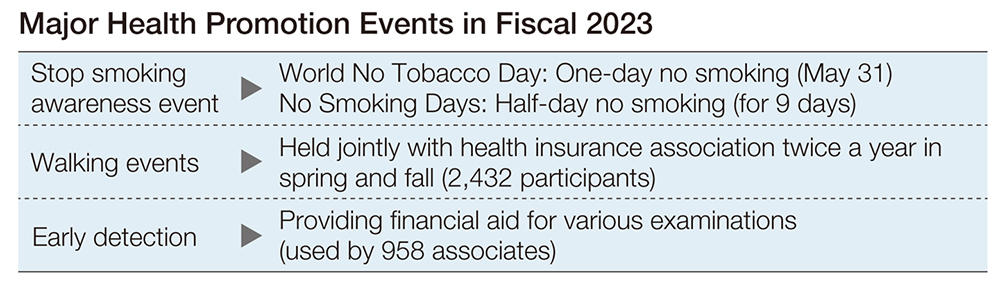
Mental Health Support
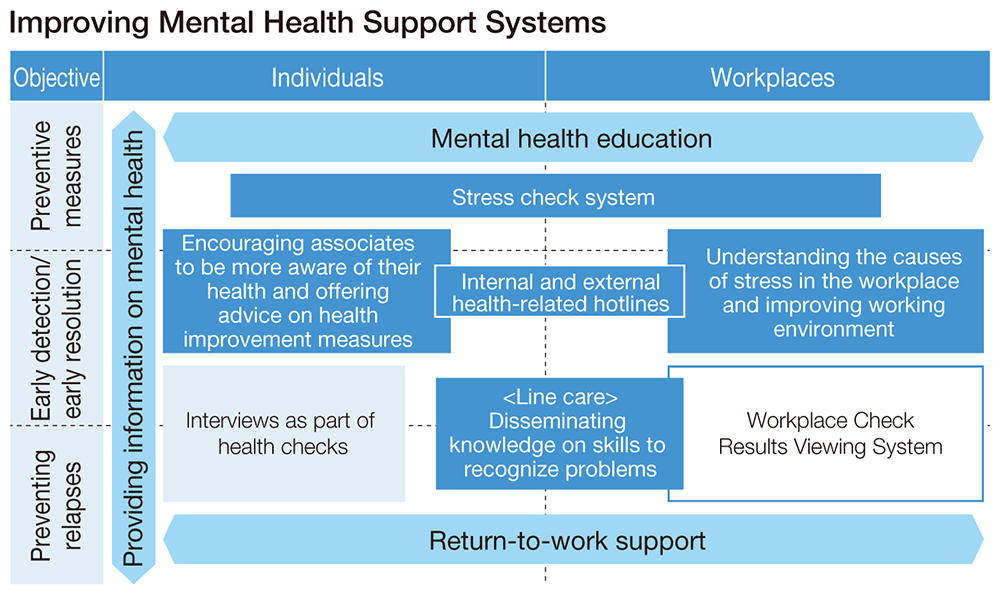
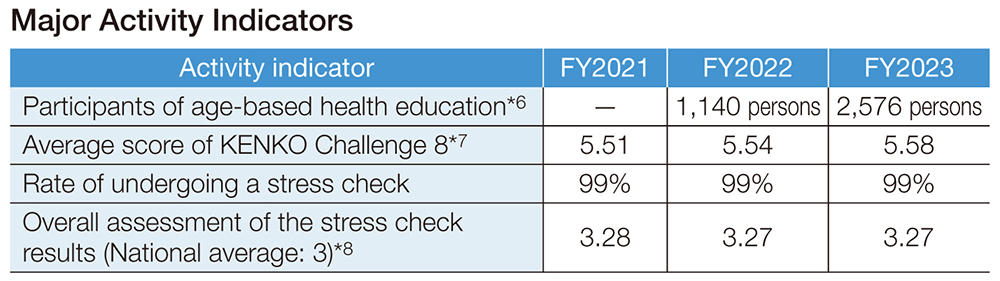
*6: Temporarily suspended from March 2020 for prevention of COVID-19. In 2021, held only during the period from July to December.
*7: Average score at which associates are practicing the eight health habits (1. Desirable weight, 2. Breakfast, 3. Snacks, 4. Sleep, 5. Exercise, 6. Alcohol consumption, 7. No smoking, 8. Stress level) (Scale of 1 to 8)
*8: Assessed using the conversion table of raw scores of the Brief Job Stress Questionnaire (1: High stress; 3: National average; and 5: Low stress on a five-point scale)
As part of mental health support activities, we have in place a system to offer early consultation through a health-related hotline. Other activities include upgrading our self-care/ line-care education to prevent new cases of mental health problems and operating a return-to-work support program for persons on long-term leave for the prevention of relapses. We have successfully achieved positive results through these activities.
As for activities for early detection, we put particular emphasis on line care by associates’ immediate supervisors. We have been encouraging them to use check sheets to recognize the sign of a problem with their subordinates early and confirm its implementation status through interviews and questionnaire surveys. The results revealed that, coupled with an effort to strengthen the collaboration between each workplace and the departments responsible for health promotion, these activities have resulted in an increase in cases where a problem is detected early and still in the mild stage.
Additionally, we have been conducting an annual stress check on all associates since fiscal 2017. We feed back the check results to all participants and workplaces with suggestions for improvement while setting up an individual interview with a doctor for those wishing to do so, including making an individual recommendation to associates found to have a high level of stress through the internal check, and providing improvement support as necessary to individual workplaces.
Response to COVID-19
In fiscal 2023, we again provided workplace vaccinations to all willing associates at Toyota Industries facilities. As another response, we updated our Infectious Disease Response Manual as necessary in accordance with the infection alert level announced by Japan’s national and local governments, communicated the revisions thoroughly within Toyota Industries and dealt with the changing situations appropriately. Based on the experience, we have formulated the Infectious Disease Basic Business Continuity Plan, which compiles our responses to all risks anticipated upon the outbreak of a new variant of COVID-19 or an unknown infectious disease.