Customers
We strive to create a system that ensures proper manufacturing in the correct way to deliver safe and reliable products to customers.
Basic Perspective
Quality Vision Each and every member of the Toyota Industries Group complies with laws and regulations while thinking and acting from the perspective of customers at their workplaces and positions to supply appealing products/services that exceed the expectations of customers around the world, with safe and reliable quality. |
---|
In response to the incident of our legal violations in engine certification in Japan, we have reexamined the Quality Vision, which specifies our basic perspective on quality. To ensure legal compliance and deliver safe and reliable products to customers, everyone at Toyota Industries is going back to the basics and making all-out efforts to rebuild our Company-wide quality management system (QMS) so that we can offer our products to customers with confidence in quality and reassure people that Toyota Industries has been transformed in a better way.
Establishing a Foundation for Quality Governance
In January 2023, we reorganized the Quality Control Department into the Quality Management Department in order to reinforce the horizontal alignment of our quality functions. Under the Chief Quality Officer (CQO), a newly established position in January 2024, the Quality Management Department has been taking the lead in establishing a quality control infrastructure and strengthening our check function for our business divisions.
With regard to the quality control infrastructure, we will establish quality-related document formats, a system to manage quality data and knowledge, a management system for quality-related personnel and a structure to provide quality-related education. The Engine Division will spearhead the effort to revamp the existing standards and provide rules and standards for important processes needed to ensure compliance with laws and regulations. These activities will then be extended throughout the Company. As for a design review (DR), which serves as the basis of our new product development, we have reexamined the Company-wide rules and initiated the process of redefining divisional rules. We are also reviewing our quality control education to again cultivate quality compliance awareness.
As for strengthening our check function for business divisions, we have set up lines of reporting related to quality issues and started conducting quality management audits as a function to monitor business divisions.
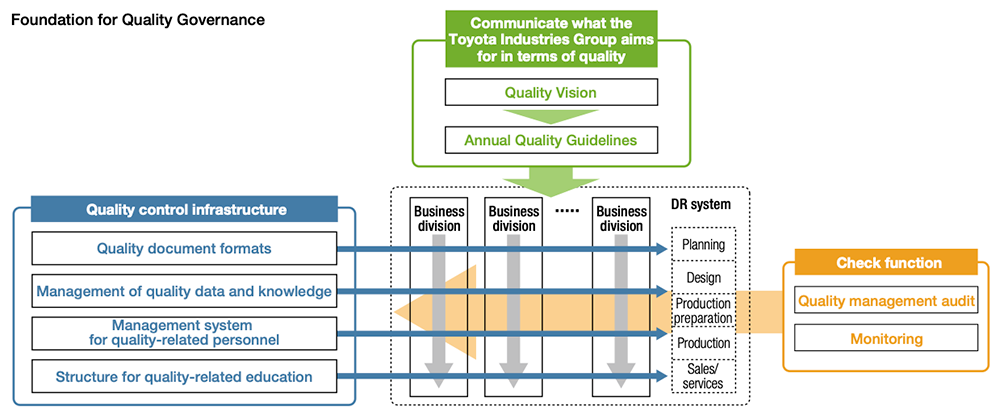
Setting up a Structure to Enhance Quality Awareness of the Entire Company
Aiming for a Robust Quality Governance Structure
For reorganizing and reinforcing our quality governance structure, Toyota Industries will promote the establishment of a new, more robust quality governance structure consisting of three check lines.
In addition to the conventional quality assurance structure of each business division (Line 1), we will set up an internal quality audit function independent of departments within each business division (Line 2). The Quality Management Department in the Head Office will audit Line 2 from a position independent of business divisions (Line 3). With these three lines, we aim for a structure invulnerable to risks.
Quality Governance Structure
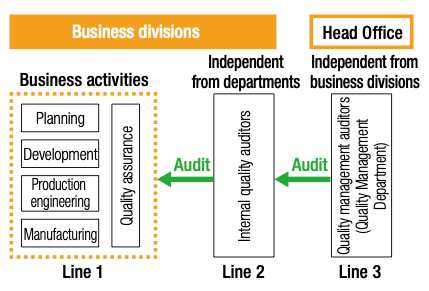
Focusing on Product Quality through Quality Management Audits
We ensure product quality while engaging all departments, from planning to development and production. One role of audit is to check this process from a third-party viewpoint to identify risks. Its scope, however, goes beyond just checking if we meet the requirements of laws, regulations and standards. It includes examining if quality-related systems and rules, which each department should follow, are working effectively and if the existing standards are appropriate as is. Additionally, by having the Head Office further check the results of internal quality audits of each business division, we expect that an appropriate check function will be exercised for prevention and timely discovery of problems.
Our newly launched quality management audits intend to enhance quality awareness of the entire Company by providing greater opportunities for more functional organizations and employees to regard product quality seriously and by encouraging everyone to become more keenly aware of the link between their work and product quality.
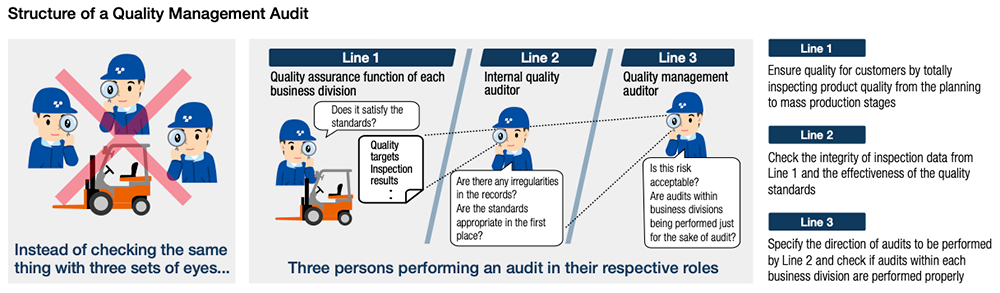
Preventing Occurrence and Recurrence of Defects
If a defect is found in a product after its launch, the Quality Assurance Department of the responsible business division takes the lead in making a swift response to eliminate the concerns of customers quickly and implementing measures to ensure the non-recurrence of the same defect. In particular, a defect causing considerable inconvenience to customers is recorded as a critical quality issue and reported to the president. At the same time, we have in place a system to follow through on customer response as well as measures to prevent recurrence. Accordingly, we examine and identify the cause by going back to its development process. We implement countermeasures both from the process and technological aspects and revise our new product development process as necessary. Through these measures, we strive to thoroughly avoid the recurrence of the defect in subsequent models. Additionally, we make efforts to prevent the occurrence of defects in all products we develop and manufacture in the future by taking measures throughout Toyota Industries.
Providing Support to Suppliers
Since improving the quality of our products requires concerted efforts with our suppliers in and outside Japan, we are strengthening joint quality assurance activities with major suppliers.
Quality Audit
In each annual quality audit, we check each business partner’s quality control status, suggest items that should be reinforced based on the results and cultivate a deeper understanding of kaizen (improvement). In fiscal 2024, following the government’s downgrading of COVID-19 classification to Class 5, we gradually shifted from remote audits to conventional genchi genbutsu (go and see for yourself) inspections and continued to check the status of quality assurance activities of each company both through a quality assurance system and on-site quality control.
Nurturing and Certifying Internal Auditors at Suppliers
To foster voluntary quality improvement efforts of suppliers, we are nurturing and certifying internal auditors at suppliers satisfying our criteria. Through these activities, we foster a culture in which suppliers work autonomously to maintain and improve their quality assurance systems and foster quality assurance on their own.
Promoting Human Resources and Workplace Development
Toyota Industries provides systematic quality education to all employees to help them acquire quality assurance skills needed in actual operations. We have been developing human resources who think, learn and act on their own while understanding that complying with laws and regulations forms the basis of our activities.
QC Circle Activities
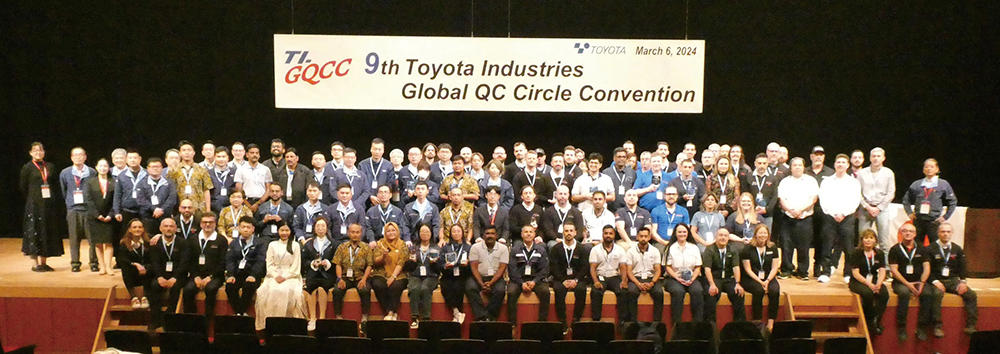
For our quality control (QC) circle activities, in which all employees participate, we have garnered many awards, as we presented the results of our activities at QC circle conventions across Japan. For example, in fiscal 2024 we received an encouragement award under the QC Circle Kaoru Ishikawa Award program for three consecutive years (for the 12th time in total). The award is given to QC circles for their distinctive activities and contribution to widespread, more active and better QC circle activities. Fiscal 2024 marked our first milestone with three of our QC circles receiving the award at the same time.
Our production bases outside Japan are also proactive in promoting QC circle activities. We assist them in undertaking independent activities by nurturing and certifying global QC circle trainers at each base. Even though the COVID-19 pandemic affected QC circle activities of all bases outside Japan, these trainers have devised creative solutions to promote, maintain and resume their initiatives. As for the Global QC Circle Convention held as a venue for presenting activity results, we hosted a video session for three years up to fiscal 2023 because of the pandemic but started holding it in Japan again in fiscal 2024. Among the Regional QC Circle Conventions hosted in respective regions, the ones in North America, Europe and China were also resumed in person in fiscal 2024 to share the accomplishments made by respective bases.
Activities to Promote Creative Ideas among Employees
All employees are striving for kaizen in their day-to-day operations through creative ideas. With regard to such ideas, we received 11 awards in fiscal 2024 in the Creativity category in the Commendation for Science and Technology by Japan’s Minister of Education, Culture, Sports, Science and Technology. These awards are given to those who have shown notable ingenuity and contributed to technology improvement.
Nurturing Human Resources Who Can Take a Scientific Approach
As part of our basic education on quality management, we teach the basics of statistical quality control (SQC) and machine learning. In order to increase the practical application of machine learning, we have been nurturing core human resources through problem solving in the workplace. We have held the TICO SQC Convention for 40 years to share best practices of each business division and hone collective skills.
■Rate of eligible employees receiving training to promote quality education (non-consolidated): 92%
Nurturing Human Resources Who Can Perform Risk Assessment of Product Safety
In order to provide products that are safe for customers to use, each business division conducts risk assessment during a DR to identify all risks. We are also providing Company-wide specialized risk assessment education to promote the development of human resources who can assess two factors integral to risk assessment, namely, the likelihood of an occurrence of a hazard and the severity of damage caused by it.